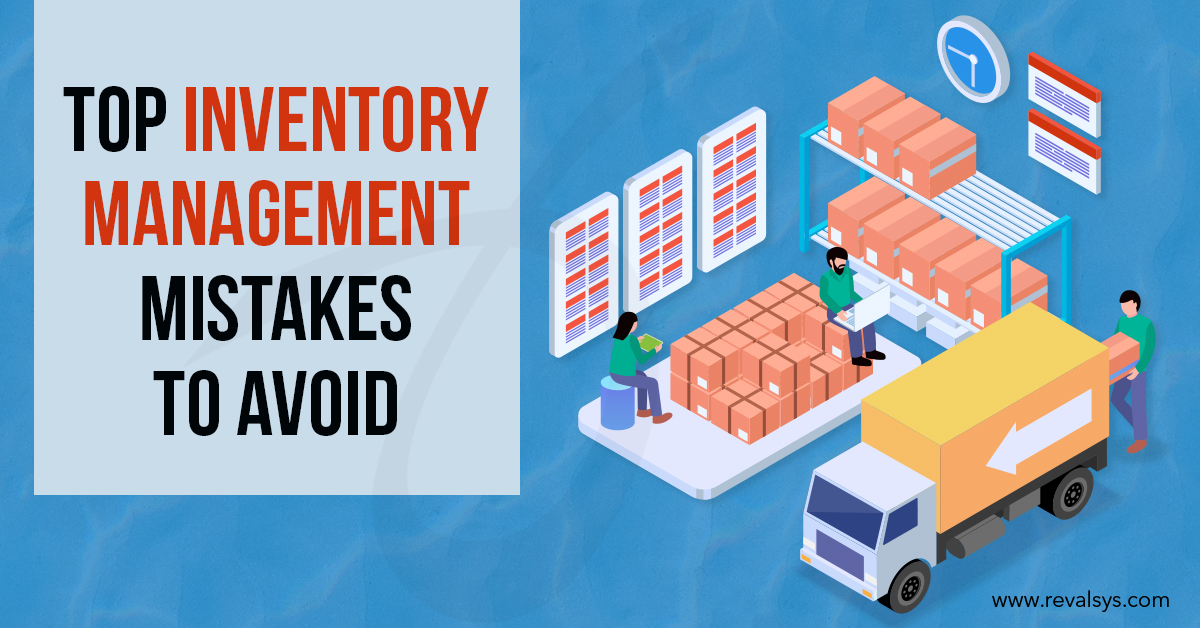
Inventory management is the process of ordering and maintaining a business’s raw materials and finished goods, and tracking their movement from the warehouse to customers’ locations. The aim of inventory management is to make sure that a business has enough inventory to fulfil all orders at the lowest possible cost. This process is important for the success of your business, no matter what its size is. Inventory management, when done well, helps you to improve productivity, save production costs, ensure customer satisfaction, and increase profits.
The key to effective inventory management is avoiding the most common mistakes, some of which we have listed below:
Not Automating The Process
The process of manual inventory management requires your employees to personally manage inventory. This means physically monitoring the movement of every piece of inventory and cross-checking physical inventory with the recorded inventory. This technique is prone to errors and causes losses as your employees can sometimes miss recording a piece of incoming inventory either because they were busy with other tasks or simply forgot to do it. An inventory management system will automate the process, speed it up, and ensure accuracy.
Having Too Much Inventory
You will be left with excess inventory when you order more stock than what is required to fulfil customer demand. Many businesses do this out of fear of running out of inventory and losing customers. However, having too much inventory is bad for you in multiple ways:
- The excess stock takes up space in your warehouse that you could use to store new stock
- The quality of the goods deteriorates and your business suffers losses
- You will have to move your inventory to a bigger, more expensive warehouse
Having Too Less Inventory
The opposite of the above scenario is equally detrimental for your business. Having too little inventory means you won’t be able to fulfil your orders on time. This will result in unhappy customers who will not only turn to your competitor but also spread negative word-of-mouth about you.
Lack Of Regular Inventory Checks
A lot of businesses use the traditional method of checking inventory physically by closing their business down for a day. This is possible when a business is small in size. However, as it grows, checking inventory physically on a regular basis while doing other tasks becomes impossible. Closing their business down frequently to do the checks also results in losses for businesses. As a result, growing companies check their inventory less frequently. This leads to inaccurate inventory forecasting, making it difficult for businesses to fulfil orders on time. When inventory checks are not done regularly, it also becomes difficult to catch any inventory shrinkage caused by damage or theft. Barcoding automates inventory tracking, thereby saving time, manpower, and money for businesses.
Workplace And Warehouse Being Located Far Away From Each Other
When you don’t work near your inventory and don’t see it regularly, you might get disconnected from it. This will make it difficult for you to check and plan your inventory levels. If it is not possible for you to have your inventory close to you and personally monitor your inventory levels, you should keep in touch with and regularly visit your team members to know the status of your inventory.
Not Storing Inventory Properly In The Warehouse
The way you store your goods plays a crucial role in their sales. When your inventory is not organised properly, your staff will find it difficult to locate goods. You will also not have space to store all of your inventory. As a result, your deliveries will get delayed and your customers will get disgruntled. Labelling your goods clearly and designating a separate storage area for your most sold items will make it easy for you to find them and fulfil your orders on time.