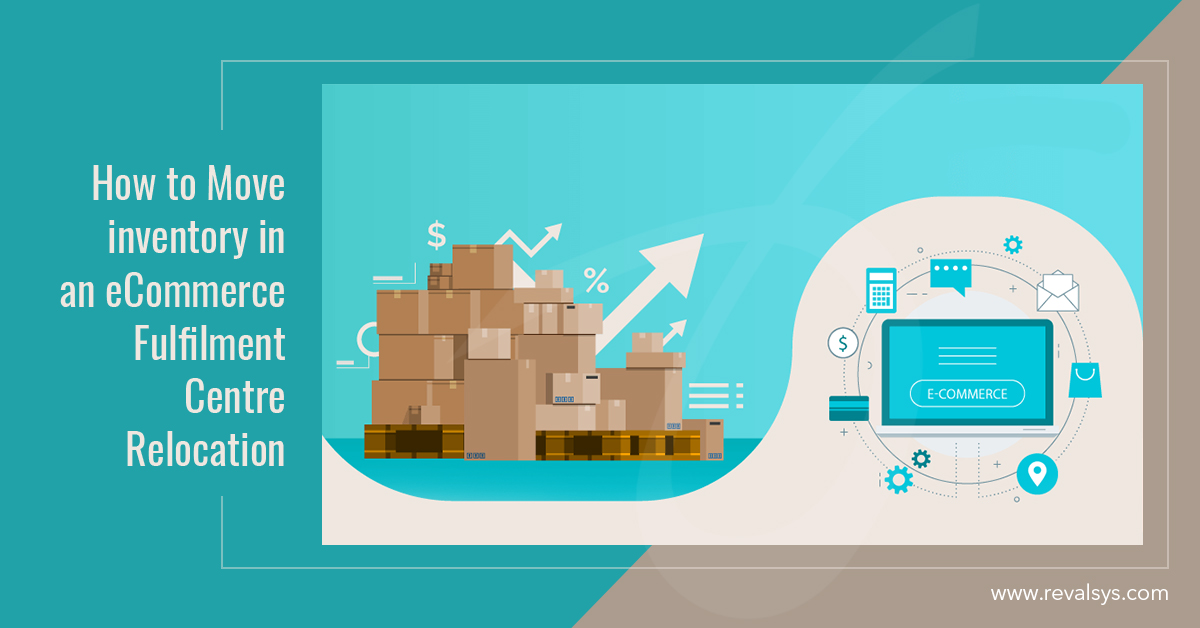
eCommerce fulfilment centre relocation is a huge undertaking that requires proper planning and execution. Things such as making the budget for start-up costs, one-time costs and the ongoing expenses are itself a tough work. And the biggest challenge of this undertaking is the disruption that occurs in your business.
During the first few weeks or months after the relocation of the fulfilment centre, the operation of the new location may be hampered severely by various inventory issues. The issues may include:
• Transferring of old inventory and overstocks rather than liquidating.
• Failure to buy and receive inventory at the new location.
• Unable to find stocks.
• Inaccurate inventory leading to problems while fulfilling orders.
Let’s check some helpful tips that make moving inventory easier in eCommerce fulfilment centre relocation:
• Determine how much space will be required
It’s important that you estimate the amount of space you’ll require in your new warehouse by identifying the number of bulk and forward picking positions. Based on the number of SKUs, you can determine it.
• Make lower overstock inventory
It’s seen that many warehouses hold old and slow-moving inventory as the owners are reluctant to liquidate those. While making fulfilment centre relocation, make sure to reduce the overstock products. You can clear all return-to-vendor inventories to eliminate the excess inventory.
• Dispose of damaged goods
There may be certain products in your eCommerce fulfillment centre which you may not be aware of. But if you find such products during inventory count process and consolidation, make sure to dispose of the damaged products if the products are not saleable.
• Estimate transportation need
When you start planning for your fulfillment centre relocation, determine how many trucks will be needed, the time required to do move the inventories and the expenses required to make the transfer.
• Create a slotting plan
One of the most critical tasks of eCommerce fulfillment centre relocation is determining where the products will be placed in the new facility soon after the goods reach its new destination. You can use data from your system to analyse things such as rate of sale, unit sales velocity, units on hand etc. You should also keep in mind about the peak season inventories while making space planning. Labelling each pallet with the new location makes it easier to keep inventory in the new centre without making another counting.
• Identify the new slot locations
Make sure to write down the quantity, SKU number, old slot location and new slot location on the pallet of the inventory ticket once you’re done with counting and consolidating the stock keeping units. And if the pallet consists of different products, write the information on each carton.